
The complete autonomous way of cleaning
solar plants!
Introducing LOTUS-A4000, a fully-autonomous and waterless solar panel cleaning robot. It's an intelligent, independent, and one of the most advanced ways of cleaning a solar plant. Each robot is dedicated to every solar row with its own solar charging-based docking station. LOTUS-A4000 is the ultimate reliable and hassle-free solution to daily clean and maintain solar plants operating in harsh and arid regions.

Upto 10% more generation output than bi-weekly cleaning
LOTUS A4000 cleaning system is based on ultra-soft microfiber cloths rotating along the length direction of the robot. The microfiber cleaning fins generate airflow and a controlled impact that flicks off the dust particles from the panels without any scratching or dragging.






Cleaning via airflow + flicking action
​​
Durable microfiber cloth with up to 2 years of life
​​
Easy microfiber replacement upon end-of-life
​​
Up to 98% cleaning in a single pass
​​
Customizable brushes for other types of dust
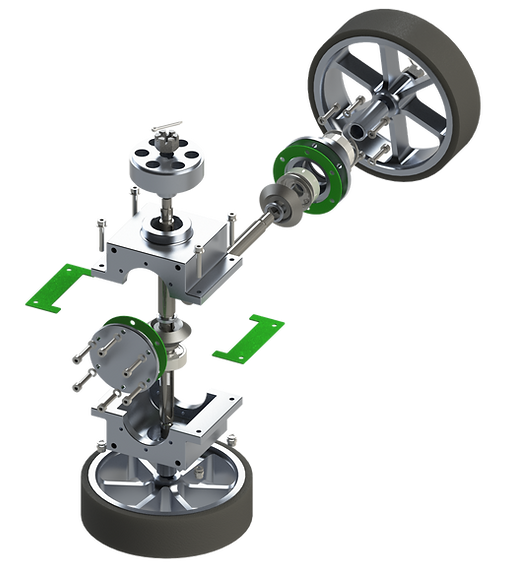
Machine Design
Our attention to detail and support from IIT Delhi has resulted in a precision-engineered machine that delivers performance while consuming less power.

Patented Technology
We have patented our unique dual-drive system with real-time orientation control which helps to overcome the module irregularities upto 40 mm.
This aluminum and steel-made drive-unit is custom-designed to be strong and lightweight.

Materials
High-grade aluminum & stainless steel is used in parts and fasteners to achieve exceptional durability and corrosion-resistant product.

Motors
High-performance BLDC motors provide 5000+ hours of life under extreme conditions with high power to weight ratio and zero maintenance.

Frame
Our robots have a rigid open-body frame which doesn’t slack while lifting and produce minimal shading with stable operation under 50 kmph wind.

Precision Engineered
The precision engineered parts provide desired features of high strength and reliable operation while minimising the weight and power loss.
Our robots have passed multiple outdoor and indoor tests of 100 + hours of continuous-operations in IIT Delhi's facilities.

Outdoor tests


Indoor tests
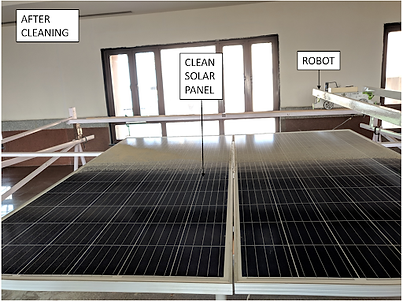.png)
See it in action
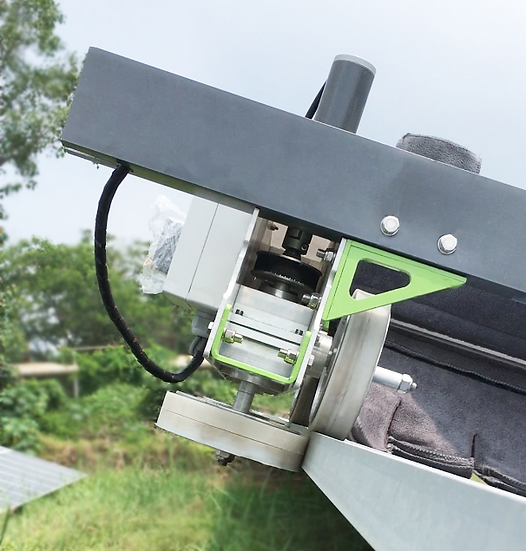
Maintains the SAFETY and INTEGRITY of solar PV module

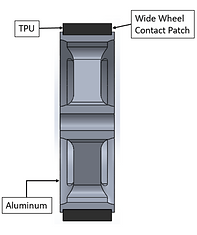

-
The wheels of the robot run on module frame to transfer the load from the frame to the underlying structure.
-
Microfiber cleaning fins flicks-off the dust and debris to prevent any damage to the Anti-Reflective Coating (ARC).
-
Appropriate hardness of the wheel coating material (TPU) provides cushion as well as durability.
-
In-lab simulations result in a Factor-of-Safety (FOS) value of 5.62.
All robots are equipped with automotive-grade
electronics and 4G based communication system

Performance
- ARM Cortex M4 based processor
- 4G LTE communication system
- Low current consumption
- High-endurance parts and switches
- Noise & Interference cancellation design
- Advanced firmware
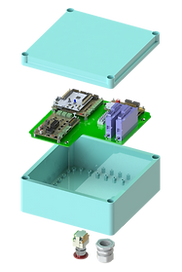
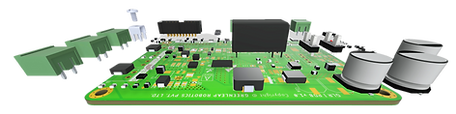

Safety
- Automotive grade Q1 components
- Extended temperature operation
- Over current & voltage protection
- Lightning surge protection
- Impact-resistant enclosure (IK 07)
- RoHS and CE certified parts
- IP65 ingress protection
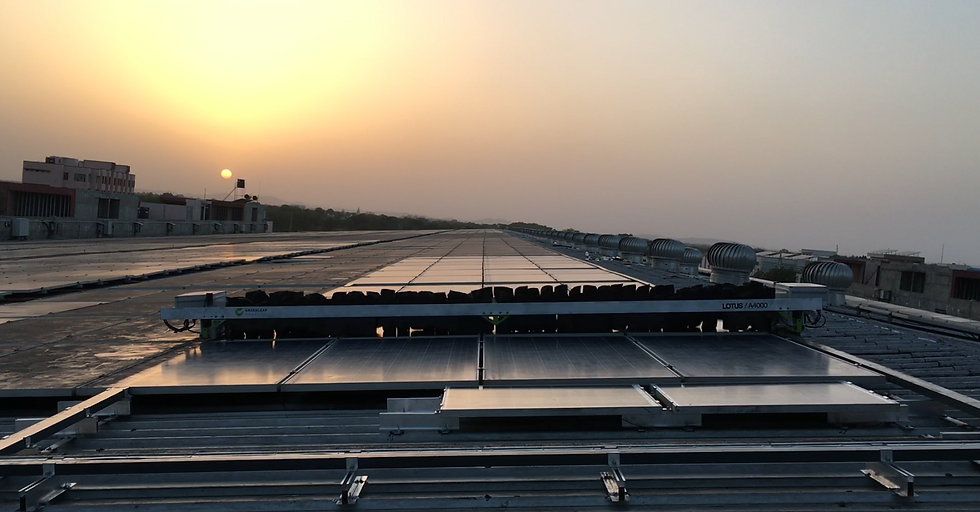
Longer cleaning time with lesser battery size

A single cleaning cycle of a standard 1 MWp solar plant is done under 2.5 hours!
Upto 3 hours of cleaning time with 12Ah @ 25.6V (Std. range)
Upto 4.5 hours of cleaning time with 18Ah @ 25.6V (Exd. range)

The Docking Station

The docking station at the end of the row is the resting and charging spot for the cleaning robot when it is not cleaning. It houses a self-executing charging connector that automatically latches when the robot arrives.





Solar-based charging
​​
Full charge under 2 hours
​​
Robust charging connector​
​
Rooftop and ground-mount compatible
​
All weatherproof
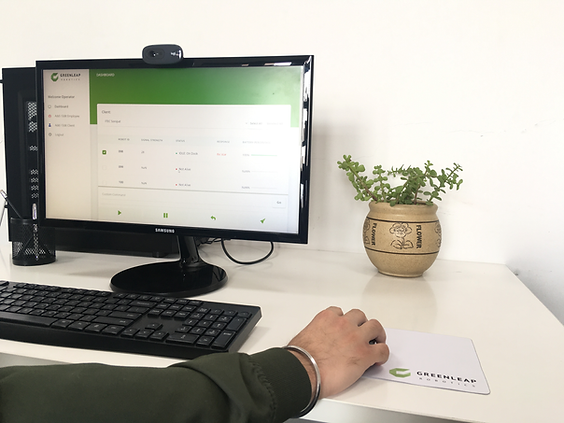
Dashboard

Real-time monitoring

Error notification

Report generation
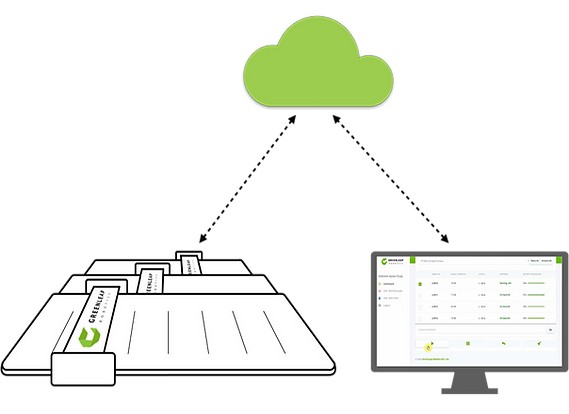
ROBOTS
All LOTUS-A4000 robots are centrally managed and controlled via our proprietary web application. This ensures peak performance, zero downtime, and predictive maintenance of all the robots.
Tier-1 Suppliers


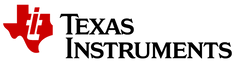


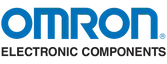



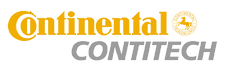




